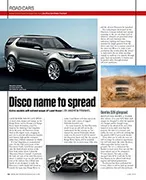
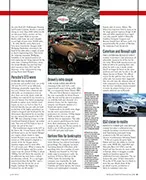
Road car news
Disco name to spread Extra models will extend scope of Land Rover | By Andrew Frankel Land Rover has of late spent so much time, money and energy on the…
SECRETS OF ENGINE BALANCE—continued.
Apart from the flywheel, which, if accurately machined, is seldom much out of balance, the only revolving component with any considerable inertia is the crankshaft. The centrifugal force set up by a single throw crankshaft when revolving at considerable speed is transmitted to the crankcase and tends to set up stresses, which if not counteracted would create very severe vibrations. To obviate such stresses a single throw crankshaft must be balanced by the provision of counter weights, extending radially in the opposite direction from the throws, and so proportioned that when rested by its main journals upon knife edge supports, it will remain at any position in which it is placed. In other words its static balance is correct, but here we are confronted with one of the fundamental problems of engine balance, which arises from the difference between the static and dynamic balance of rotating parts.
After all, where an engine is called upon to develop its maximum power at high speeds, the dynamic balance is the more important and many engine builders insist upon having their crankshafts with a correct dynamic balance, say at 2,500 r.p.m., even though at L000 r.p.m. it may be slightly out of balance. The argument put forward is that at low engine speeds the bearings are capable of resisting any possible distortion due to imperfect balance, but at high speeds nothing short of perfection will give the maximum efficiency.
Influence of Crank Design upon Balance.
With the symmetrical design of a four-throw crankshaft it might be supposed that little difficulty would be experienced in obtaining both static and dynamic balance in equal degrees, but in practice such is seldom found to be the case, because as the speed of rotation rises there is nothing to prevent a certain amount of distortion between the webs. Unless balancing counterweights or extended webs are provided one has to choose between static balance when the crankshaft is stationary, or dynamic balance when it is rotating, the only test for the latter is carried out by the aid of the balancing machine.
Action of the Crank Balancer.
The crankshaft balancer consists in a tubular base mounted on suitable supports, one of which provides a housing for an electric motor, driving a shaft running parallel to the tubular base. The vertical supports upon which the crankshaft to be tested is mounted are adjustable in a lateral direction to accommodate crank shafts of different dimensions and at their upper extremities are fitted with rollers to receive the crankshaft journals.
A belt is passed over one of the main journals as shown, and when the motor is set going the crankshaft revolves, its speed of rotation being controlled by a resistance switch. Now, if the crankshaft is out of balance, its vibration will affect the vertical supports, which are free to vibrate within certain limits, this movement being clearly indicated by means of a pointer working over a dial on each of the vertical supports. Thus, at the first test, we may discover that a crankshaft which has been machined all over is considerably out of balance, and besides creating the possibility of
marked vibrations in the engine for which it is intended, would if uncorrected be responsible for an excessive amount of wear on the bearings. The use of the pointers mounted on the balancing machine may be appreciated when tests are made with balanced and unbalanced crankshafts. In the latter case, the pointers will flicker violently at speeds as low as 250 r.p.m., but after the balancing process has been completed the crankshaft speed can be increased to 2,000 r.p.m. without causing the slightest movement of the pointer. Whilst engine speeds are frequently much in excess of the latter figure, there is no practical necessity to worry much about balancing the crankshaft for the maximum rate of revolution as experience proves that if the balance is correct at about 2,500 r.p.m. the shaft will run quite steadily at the higher speeds ; provided, of course, it possesses sufficient rigidity to resist the natural distortion set up by centrifugal force.
Method of Correcting Crankshaft Balance.
With all the improvements in balancing machines, no method has been devised for eliminating a certain amount of ” trial and error “work in correcting inaccurate crankshafts. The flickering of the pointers will show the extent to which a shaft under treatment is out of balance, and the operator then commences to tie small lead weights on various parts of the throws, until a correct balance is secured on testing the shaft on the machine. It may take several attempts to determine the correct position and weight of the lead pieces thus added, but after this is done, a correct balance can be obtained by removing metal, corresponding in weight to the lead pieces, at positions opposite to those at which the trial weights were affixed.
Flywheel Balance. As mentioned previously, the flywheel should not be much out of balance, if properly machined ; but it is curious to observe the number of cases where lack of flywheel balance is found.. I have recently come across quite a number of engines in which the flywheel balance could only be made perfect by the removal of a pound in weight, the fault being due to the imperfect machining